top of page
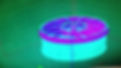
Investment Casting Precision Prototypes
Low volume. Quick turnaround.
CAST METAL PROTOTYPING
Wondering what’s possible?
We specialize in turning ideas into reality within days. Invest Cast offers complete prototyping capabilities in a wide variety of metals, without tooling, in as little as 48 hours. As the largest and fastest producer of cast metal prototypes in the country, we utilize our in-house expertise along with a tight-knit group of engineers and designers who are able to help meet all your unique prototype needs. Our experienced staff is happy to work with you to figure out how to get the best prototype possible, in the shortest amount of time.
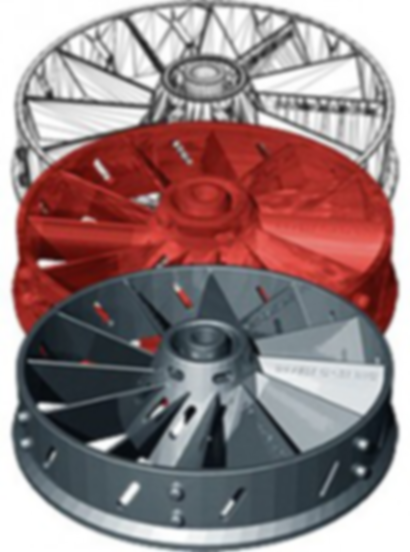


HOW IT WORKS
Prototype Casting Process
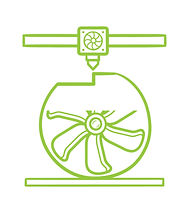
SLS Pattern Creation
The first step in the prototype casting process is to build an SLS pattern directly from a CAD file. This can be completed in just hours without tooling.
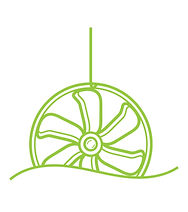
No need for tooling
The pattern is then prepared for production by coating the part in wax. From here, we use our normal process to create a production quality part.
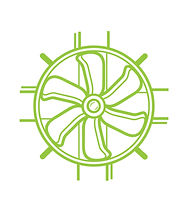
Wax assembly
Patterns are “wax welded” to a central sprue or cluster to facilitate pouring. Many patterns are attached to sprues for increased efficiency
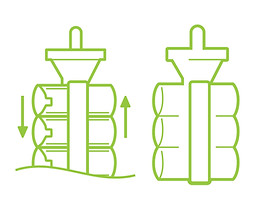
Shell Building
The assembled sprue is then dipped into a ceramic slurry. After draining, the sprue is then coated with a fine silica or stucco sand. This process is repeated several times using progressively coarser grades of ceramic material to build sufficient “shell” strength.

De-waxing
The shell built sprue is then de-waxed by rapidly heating in a furnace or autoclave, leaving behind the perfect shell cavity free of wax.
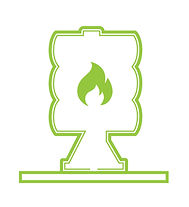
Preheating shell
The shells are then fired at 1600° to 2000°. This cures the shells interior into a smooth, hard and strong ceramic material.

Pouring
The sprues are then removed from the furnace to have the molten metal poured into them. Once the shell is filled with metal, it needs to cool and have the shell material removed from the outside of the casted parts.
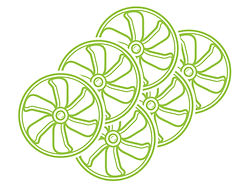
Part Finishing
Once clear of ceramic shell, the cast parts get cut off from the sprue, then they are brought through a number of finishing processes. These processes include various cleaning stages, grinding, plating, machining, and heat treat.
bottom of page